AMR(自律走行搬送ロボット)とは|AGVとの違いからわかる導入メリットとメーカーの動向
人手不足対策や生産性の向上が急務とされている物流倉庫や製造現場にて、AMRの導入が進んでいます。倉庫内などで使われる搬送車の種類にはAGVなどもありますが、AMRはどのような違いや特徴があるのでしょうか?
自律走行搬送ロボット「AMR」を導入するメリットや、メーカーの動向、導入事例などを紹介していきます。
- AMR(エーエムアール)とは「自律走行搬送ロボット」のこと
- 走行ルートの自動算出・自律走行が可能であり、人と協働できる
- AMRの導入は省人化・業務効率化につながる
目次
自律走行搬送ロボット「AMR」とは
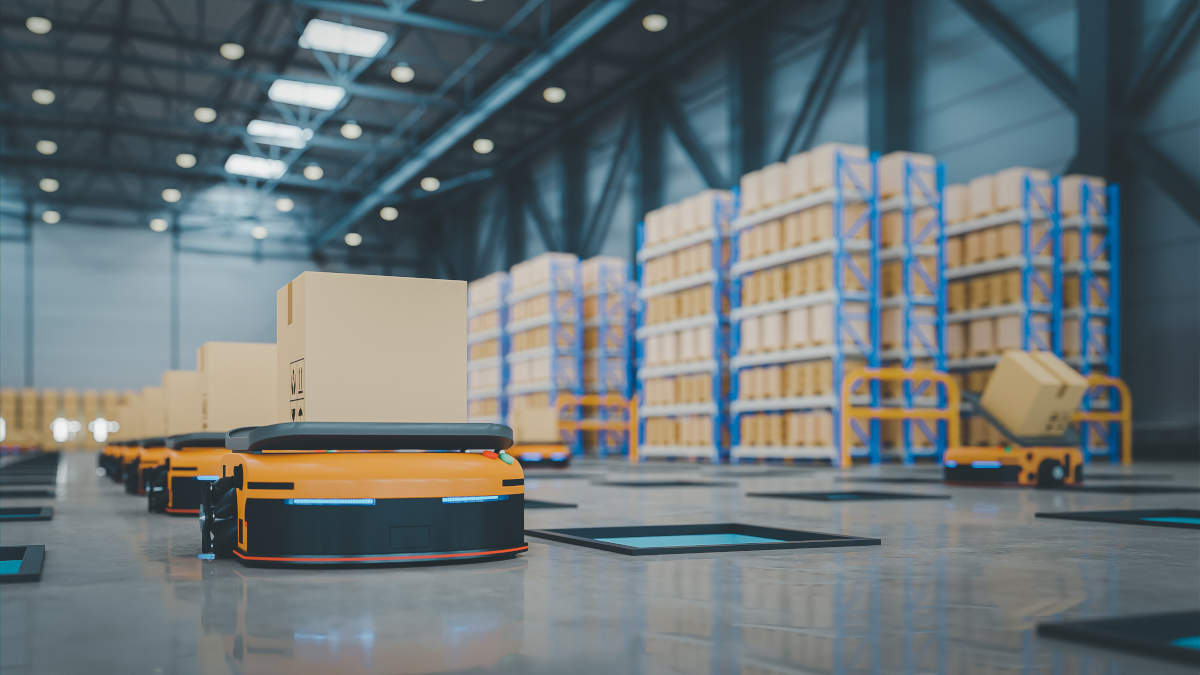
AMR(読み方:エーエムアール)とは、「Autonomous Mobile Robot」の略称の「自律走行搬送ロボット」です。
AMRは「次世代AGV」として製造業界や物流業界を中心に注目を集めており、物品の搬送を行うタイプのほか、ピッキングのサポート機能を付帯したカートタイプなどの種類も登場しています。
AMRとAGVの違い
倉庫内で無人で搬送を行うロボットや機械には、AMR以外にも従来から活用されてきたAGV(無人搬送車:automatic guides vehicle)があります。
両者は類似点もあることから混同されがちですが、「走行ルート」「障害物対応」「人との協働可否」における明確な差分があります。
AMR(自律走行搬送ロボット) | AGV(無人搬送車) | |
走行ルート・移動範囲 | 自動算出によるルート・自律走行 | 固定されたルート・誘導走行 |
障害物対応 | 回避・再ルーティング | 停止 |
人との協働 | 可 | 不可 |
AGVは、磁気テープなど床面の誘導体によって設定された固定ルートを走行する誘導走行により、物品を搬送します。
これに対して、AMRは誘導体が不要。センシング技術などによって自己の位置を推定し、目的地までのルートを自動算出して自律走行するという大きな違いがあります。
また、AGVはルート上に障害物があった場合には停止し、そのまま走行を続けることができません。
一方、AMRは障害物を回避し、再びルートを自動算出します。こうした特性から、AMRは人と稼働範囲を共有しての協働も可能です。
AMR導入のメリットとデメリット
自律走行や障害物の回避など明確な強みを有するAMRですが、実際に導入するにあたってはクリアすべきいくつかの課題もあります。
AMR導入のメリット | AMR導入のデメリット |
●人と協働しやすい ●作業環境の変化に柔軟に対応しやすい ●作業者の移動距離を抑えられる ●ヒューマンエラーを削減できる ●作業の効率化よる生産性の向上を図れる |
●多額の導入コストがかかる ●ロボットが通行するスペースの確保が必要 ●運用方法を策定する必要がある |
まず目を向けなくてはいけないのは、コストの課題です。AMRの導入にあたっては、AMR本体の費用のほか、AMRを制御するためのシステム関連費用、ネットワークなどインフラ基盤の整備費用などが必要になります。
また、AMRはAGVよりも高額で、AGVは1台100万円程度から購入できるのに対し、AMRは1台数百万円程度。1,000万円を超える製品もあるほどです。
通路スペースの確保も、AMRの運用には欠かせません。人と協働する場合には、人が通る動線への考慮も求められます。作業手順や作業エリアの区画を決めるなど、AMRの運用方法の策定が負担となることもあるでしょう。
こうした課題がありながらも、なぜAMRは「次世代AGV」と目されているのか。それはデメリットを上回る、次に挙げるようなメリットがあるからにほかなりません。
- 人との協働が可能
- 作業者の移動距離・作業負荷の軽減
- 省人化によるヒューマンエラーの削減とコスト効率化
- 作業環境やレイアウト変更への対応力
人との協働が可能
AMRは、基本的に人との協働を前提に作られている「協働ロボット」です。
AGVなど従来の搬送車や産業用ロボットの場合、ロボットや機械の作業エリアと人の作業エリアは区分されていることが一般的です。一方、人と稼働範囲を共有できるAMRは活用の幅が広がり、人との協働によってピッキングを効率化するタイプなども登場しています。
作業者の移動距離・作業負荷の軽減
従来のAGVでは、搬送ルートと人の作業エリアを分けて設定する必要がありました。そのため、作業者のすぐ近くまで物品を搬送できず、作業者が歩いて移動する工程が生じます。
一方、AMRは人と稼働範囲を共有できることから、作業者のすぐ近くまで物品を搬送し、移動距離をほぼゼロにすることが可能です。作業者の移動距離の短縮は作業負荷の軽減にもつながります。
また、ピッキングを行う物品の量が多く、手押し台車を押して倉庫内を移動するといったケースでは、その重量も負担になります。ピッキングをサポートするカート型AMRの導入で、重い台車を押すことによる作業負荷も軽減されるでしょう。
省人化によるヒューマンエラーの削減とコスト効率化
AMRによる物品の搬送業務は極めて効率的です。作業者が手押し台車で物品を運んでいるケースと比較すると、作業量は大幅に減少し、省人化が推進されます。
ヒューマンエラーの減少や作業効率のアップによるコスト削減といった効果も期待できるでしょう。
作業環境やレイアウト変更への対応力
工場の生産ラインや倉庫では、作業エリアやラック、生産ラインなどのレイアウト変更がしばしば行われます。それに合わせてAGVの搬送ルートを変更するために、誘導体の磁気テープを床面に貼り直すといった作業が都度発生していました。
これに対し、AMRは工場や倉庫のレイアウトが変わっても搬送ルートを自動算出するため、臨機応変に対応できます。
市場規模の拡大とAMRメーカーの動向
新型コロナウイルスの感染拡大による影響を一時的に受けたものの、AMRの市場規模は右肩上がりの傾向です。市場規模の進捗と予測値、AMRメーカーの動向をみていきます。
AGV/AMR搬送ロボット市場は右肩上がり
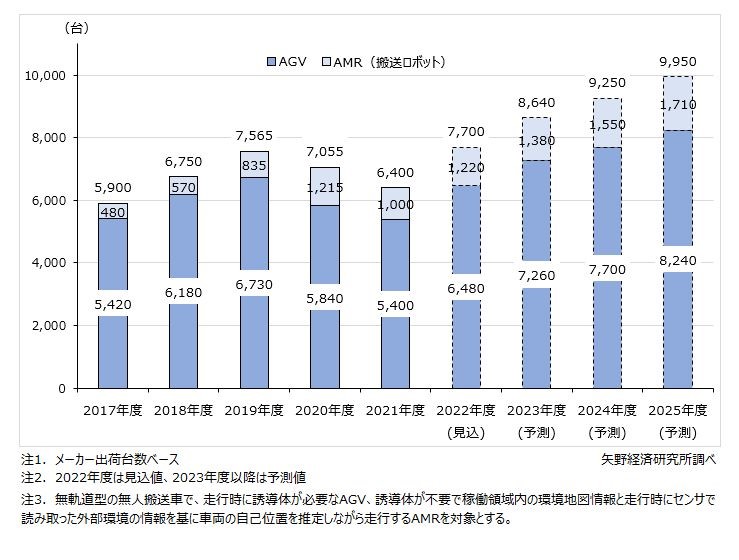
矢野経済研究所の調査によると、AGV・AMRの搬送ロボット市場は、2017年から2019年まで右肩上がりで成長しています。2020年には新型コロナウイルスの感染拡大に伴い、先行きが見通せない状況から、AGV・AMRの出荷台数は前年比6.7%減の7,055台にまで落ち込んだものの、AMRに絞ってみると前年よりも増加しています。
また、2021年も半導体不足の影響を受けたことから、AGV・AMRの出荷台数は6,400台に落ち込んでいます。
しかし、2022年以降は人手不足対策と設備投資へのニーズの高騰から、再びAGV・AMRの需要が増加していくと見込まれています。
国内外AMRメーカーの動向
ベンチャー企業も参入するなど、AMRはこれからの過熱が期待されている市場です。国内外のAMRメーカーの動向を紹介していきます。
OTTO Motors:アタッチメントを装着可能なAMR
OTTO Motorsはカナダ企業「Clearpath Robotics」の産業部門のブランドです。2020年2月に日本の産業機械・機器商社であるアルテック株式会社との提携により、日本市場への参入が発表されました。
OTTO Motorsでは、最大積載量の異なる3機種のAMRを展開しています。
- OTTO100:最大積載量150kg
- OTTO750:最大積載量750 kg
- OTTO1500:最大積載量1,900kg
OTTO750とOTTO1500では、オプションでパレットやコンベア、リフターといったアタッチメントの取り付けも可能です。
OTTOシリーズの制御には、マテリアルハンドリング専用の管理システム「フリートマネージャー」が用意され、システムの面でも定評があり、物流業界で広く採用されています。
ラピュタロボティクス:ピッキングの作業効率の向上に貢献
ラピュタロボティクスは、チューリッヒ工科大学の出身者を中心に設立されたベンチャー企業です。
創設者2名が日本に留学していた経緯から、2014年に東京都江東区に本社を構えて設立されました。エンジニア部門はカナダに置かれ、2016年にインド・ベンガルールに支社を開設。2019年に物流市場へ参入しました。
「ラピュタPA-AMR」はピッキングの生産性向上を図れるAMRです。同機はピッキングを行う場所に移動し、棚の位置を指示して作業者がカートに物品を入れると、次の作業箇所を指示して先回りをします。担当するエリアのピッキング作業が終わると、次のカートが来ているため、荷下ろしの場所まで歩く必要がなく、作業者の負担を大幅に減らせる仕様です。
ラピュタロボティクスのAMRは、大手物流会社や通販会社などで採用されています。
寺岡精工:作業者との協働によりピッキングを効率化
寺岡精工は1925年に創業した老舗メーカーで、POSレジや計量器、ラベルプリンター、食品包装機、ピッキングカートなど、流通業界や物流業界に関わるさまざまな製品を取り扱っています。
寺岡精工のAMRもピッキングをサポートする機能が付加されたタイプです。同社の自律走行式ピッキングカートは、作業者の移動経路が最短となるように経路を算出して、倉庫内を自律走行。作業者は画面の指示に従ってピッキングを行うなど、ピッキングカートと協働する仕組みです。
また、コンテナの物品量によっては、別のピッキングカートが空コンテナを運び、作業者の移動負荷を抑えています。
グラウンド:トリプルチェックによる精度の高いピッキングを実現
グラウンドは2015年に設立された、ITテクノロジーを活用した物流ソリューションを提供する企業です。
ダイオーエンジニアリングとの共同開発による「PEER SpeeMa+」は、ピッキングの作業効率と精度の向上を図るAMR。カートに搭載されたタブレットの指示に従ってピッキングした商品をカートに入れると、RFIDリーダーがタグを読み取り、正しい商品が投入されていると、次のピッキング場所に移動する仕組みです。
タブレットの指示、RFIDによるチェック、作業者の目視のトリプルチェックを行えるため、精度の高いピッキングを実現できます。
AMRの導入事例
AMRの導入によって、実際にどのような効果がもたらされているのか。AMRの4つの導入事例を紹介していきます。
佐川グローバルロジスティクス:AMRの導入により1日の処理件数が向上
佐川グローバルロジスティクスは、佐川グループの中で3PL事業を手掛けている企業です。
同社のAMR活用は、BtoB商材の出荷管理を行う物流倉庫で実験的に導入したことから始まります。導入の背景には、人手不足対策と長時間労働の是正のほか、ロボットの導入事例を作る目的もありました。
お客様からの出荷依頼にリアルタイムで対応する体制は、AMRの導入後も大きく変わることなく運用できており、1日の処理件数も大幅に上昇するなど、導入実験は成功。運用実績を踏まえ、他拠点での導入も進んでいます。
アスクル:365日稼働する現場でピッキングの効率化を実現
台車を押しながらハンディターミナルを持ってピッキングする、従来的な方法を採用していたアスクルでは、生産性の向上が課題となっていました。しかし、倉庫は365日稼働しているため、大規模なレイアウト変更は困難です。そこでAMRの導入に至りました。
導入したAMRは、ピッキング作業が終わると次のAMRが来る場所が表示するタイプ。AMRを探す手間もかからないことから、導入によって効率よく作業を進められるようになりました。
また、ピッキングとピッキングの間の歩行距離も短縮されました。カートの荷下ろしは専門のスタッフを配置し、ピッキングの担当者はピッキングに専念するなど、分業制をとるきっかけにもなっています。
日本通運:AMRによってピッキングに集中できる環境を構築
日本通運では、空調機器メーカーの保守用パーツなどの保管・配送を行う物流センターでAMRを導入しました。2万3000点もの膨大な品目数を抱え、閑散期では1日あたり約1,500件、繁忙期には1日約5,000件ものピッキングを行うことから、スタッフの勤務時間の超過が問題となっていたためです。
そこで、7~8名程度のスタッフに対して、AMR10台を導入。細かい保守部品を配置している区画にAMRを導入し、AMR5~7台に対し3名作業者を配置する体制をとっています。
作業者はハンディターミナルを持ったり、台車を押したりする作業がなくなり、ピッキングに専念できるようになりました。導入によって作業スピードがアップするだけではなく、精神的な負担も軽減されています。
トラスコ中山:工程間搬送の効率化を実現
機械工具などを扱う専門商社のトラスコ中山では、工程間搬送の距離の長さや重量物を運ぶことによる作業負荷により、搬送が滞るという課題を抱えていました。
そこで、AMRを導入し、工程間搬送を自動化してフロアでの滞留を改善。また、産業用ロボットのひとつであるパレタイズロボットとの連携によって、仕分けから出荷場への搬出までの作業の自動化を実現しています。
まとめ
製造業や物流業の多くの企業では、人手不足は慢性的な課題となっています。課題の解消と競争力の強化を図るためには、業務効率化による生産性の向上が欠かせません。
AMRの導入は、省人化や業務効率化の実現につながるものです。物品の搬送を自動化できるだけではなく、ピッキングのサポート機能が付帯されたカートタイプはピッキングの効率向上にも貢献します。
コスト面の課題などを無視することはできませんが、長期的視点に立ち、経営上の課題の解決に結びつくか検討してみましょう。