QC7つ道具とは?「新QC7つ道具」との違いと品質改善に活用する手法
製造業の品質管理では、製造工程や品質に関わるさまざまなデータを収集し、数値データの整理・分析を通じて発見された課題の見える化を図ります。こうした品質管理の手法として代表的なものが、「QC7つ道具」です。
QC7つ道具とは何か、それぞれの手法について取り上げるほか、「新QC7つ道具」についても触れていきます。
- QC7つ道具とは、製造工程や品質などの数値データを整理・分析する手法の総称
- QC7つ道具はパレート図、特性要因図、グラフ、ヒストグラム、散布図、管理図、チェックシートを指す
- 問題解決のフェーズによって適切なQC7つ道具は異なる
目次
QC7つ道具とは
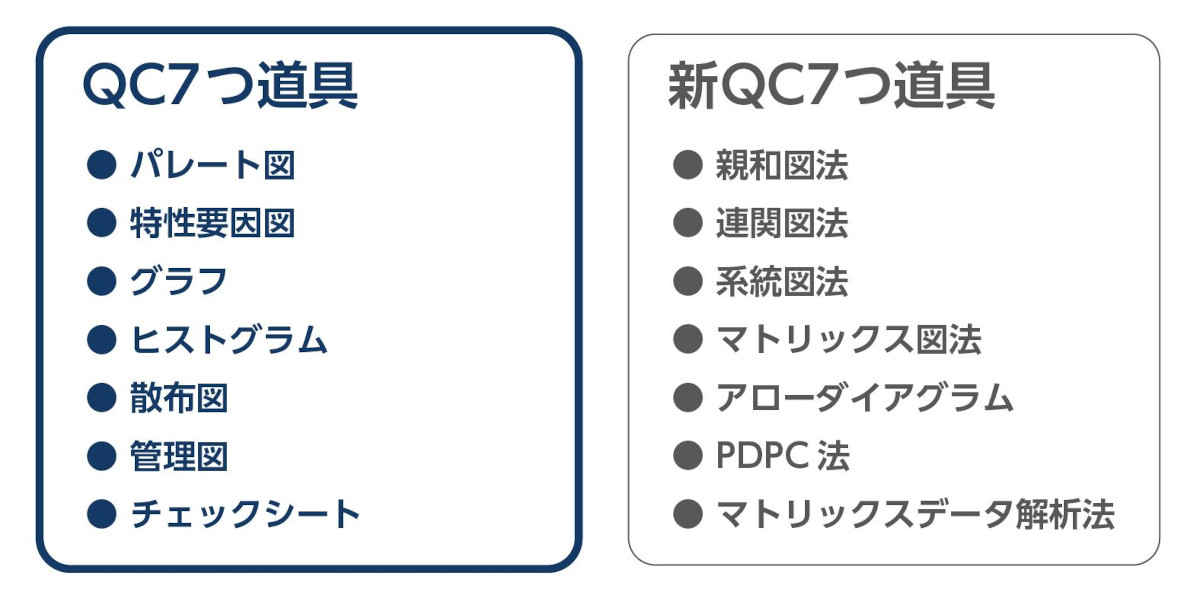
QCは「Quality Control」の頭文字をとった略語で「品質管理」を意味し、顧客の要求水準を満たすために、一定の品質を保つよう合理的に管理することをいいます。
つまりQC手法とは、合理的に品質管理を行っていくための手法です。現状を把握して問題を発見、その原因を分析し対策・改善、効果検証を経て定着化させるというプロセスで実施していきます。
そしてQC手法の代表的なものとして挙げられるのが、「QC7つ道具」や「新QC7つ道具」です。
QC7つ道具とは、製造工程や品質などに関する数値データを整理・分析する統計的品質管理の手法の総称です。以下の7つのツールを用いることから、QC7つ道具と呼ばれています。
- パレート図
- 特性要因図
- グラフ
- ヒストグラム
- 散布図
- 管理図
- チェックシート
QC7つ道具の覚え方
QC7つ道具の覚え方としてよく知られているのは、『サンチェ監督引っ張れそう!』の語呂合わせによる方法です。
- サン:散布図
- チェ:チェックシート
- 監:管理図
- 督:特性要因図
- 引っ:ヒストグラム図
- 張れ:パレート図
- そう:層別・グラフ
やや強引ですが、サッカーや野球の外国人監督がチームを引っ張る姿をイメージしてください。
なお、ここでは先ほどの説明とは少し異なり、最後に「層別」という項目を入れています。層別は、QC7つ道具に入れる・入れない双方の考え方があるものです。
ちなみに層別とは、「たくさんあるものを特徴によってグループ分けすること」をいいます。時間別であれば「昼・夜、週単位、月単位」、作業員別であれば「男女別、班別、経験年数別」といった形のグルーピングです。
QC7つ道具を使用する目的
QC7つ道具の使用目的には、主に以下のようなニーズが挙げられます。
- 現在の状況の問題点を見える化したい
- 不良品の発生や不具合の原因を整理・分析したい
- 原因と結果の相関関係を調べたい
- 改善策を実施後の効果を検証したい
これらの目的をどのように達成していくのか、次項からはQC7つ道具の活用方法を見ていきます。
QC7つ道具の使い方・QCストーリー
QC7つ道具を品質管理に活用していく方法として、「QCストーリー」と呼ばれる問題解決プロセスがあります。

まずは問題点を抽出し、改善するべきテーマを定義します。次に、データを収集して現状を把握し、どの程度の改善を図るのか目標値を設定します。そして、問題を引き起こしている要因を解析・特定し、改善策を立案して実施。効果が実証された場合には標準化して定着させます。
このQCストーリーのフェーズごとに、主に活用できる7つ道具は次のように分類されます。
QCストーリーのフェーズ | 主に活用されるQC手法 |
現状把握・課題の発見 | ● グラフ ● 管理図 |
課題の要因を特定 | ● パレート図 ● 特性要因図 ● ヒストグラム |
効果を確認 | ● グラフ ● 散布図 ● チェックシート |
QC7つ道具のそれぞれの手法について、具体的に解説していきます。
パレート図
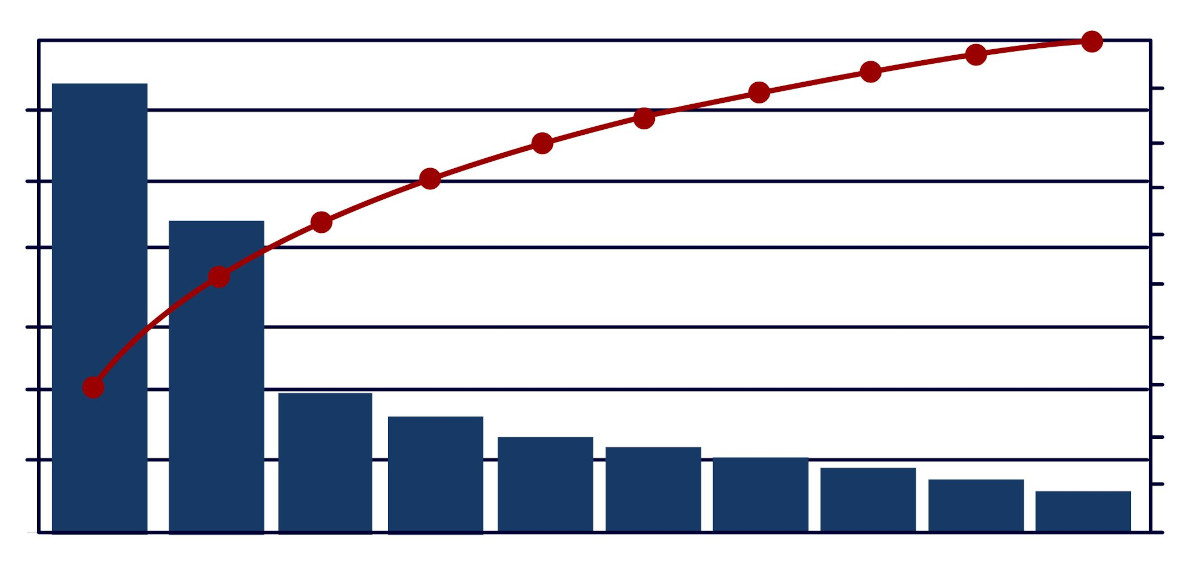
パレート図は、数値が大きい方から並べた棒グラフと、累積構成比を示す折れ線グラフを表した図です。全体のなか大きな要因を占めているものはなにか、把握したい場合に役立ちます。大きな要因に絞って重点的に改善策を実施し、効率的な課題解決につなげていくための手法です。
たとえば、不良品の発生を現状よりも50%減少させることを目標とするケースで、原因が大まかに6つある場合に、1つあるいは複数のいずれの項目の改善策を実施すれば、目標達成を見込めるか判断できます。
特性要因図
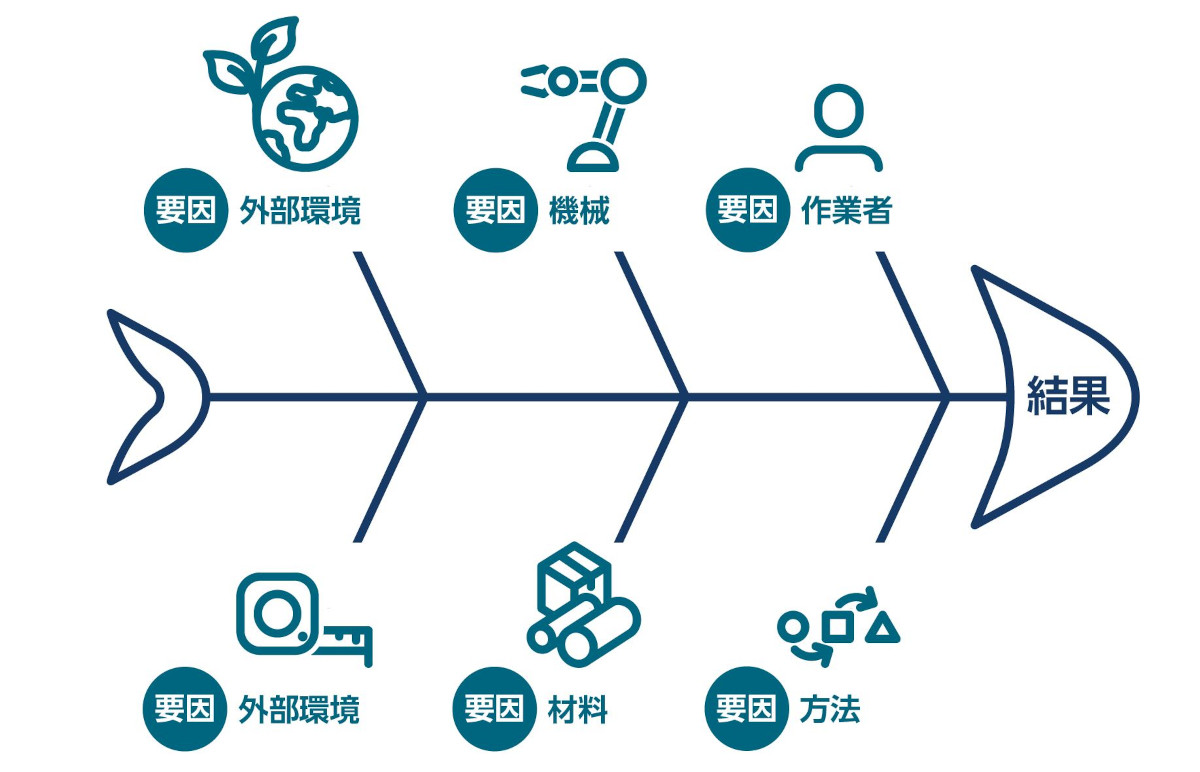
特性要因図は、ある事象を引き起こす要因を階層構造で示したものです。「特性」、すなわち結果に影響する大きな「要因」を書き出し、さらにそれぞれに関連する要因を書き出して整理していきます。特性要因図は、見た目が魚の骨に似ていることから、フィッシュボーン図とも呼ばれています。
特性要因図の作成によって、どの要因が特性に大きな影響を与えているのか、因果関係を見える化して整理し、原因の仮説を立案できます。また、導いた仮説を数値データを用いる他の手法と組み合わせて活用できます。
たとえば、「製品不良が多い」という特性に対して、「作業者」「方法」という要因を書き出し、さらにその要因を分解しながら考察していきます。
- 作業者:習熟度が低い作業者が多い
→熟練者の退職が相次いだ・社員教育の時間が十分に確保できていない
- 方法:属人的な作業が行われている
→手順書がない・手順書が遵守されていない
このような要領で、大きな要因ごとに絞り込んで、その要因の細分化を繰り返しながら原因を追究していきます。
グラフ
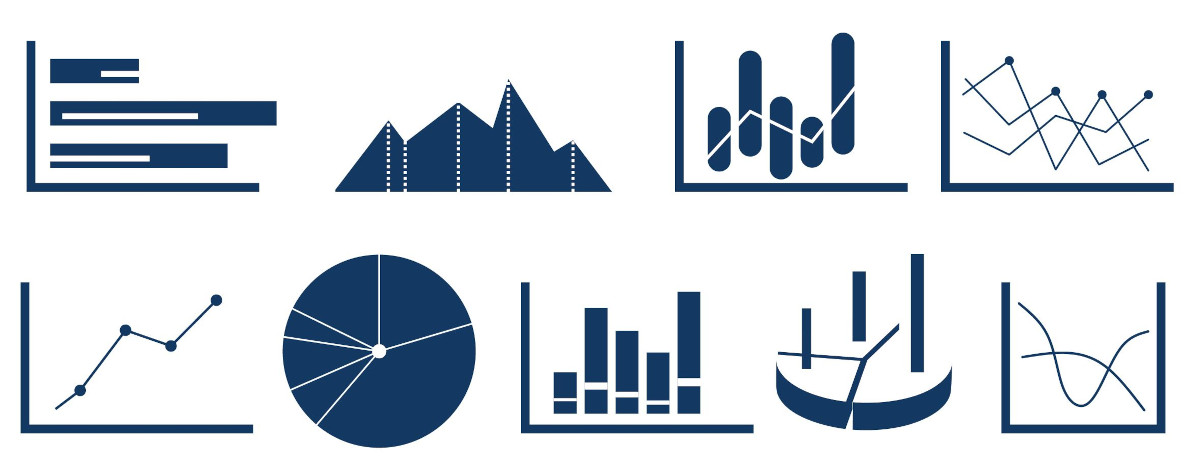
グラフはデータを視覚的にわかりやすいように、図で示したものです。いくつもの種類があるため、目的によって使い分けることがポイントです
- 棒グラフ:数量などを比較する
- 折れ線グラフ:変動を確認する
- 円グラフ:比率を確認する
- 帯グラフ:他の事柄と比率を比較する
- レーダーチャート:各項目のバランスを見る
QCにおいては、グラフは主に現状を把握するときや効果を検証するときに用いられます。たとえば、不良品の発生件数を時間ごとに把握したい場合には、棒グラフを使います。一方、部品の納入先の割合を把握した場合に向いているのは円グラフです。
ヒストグラム
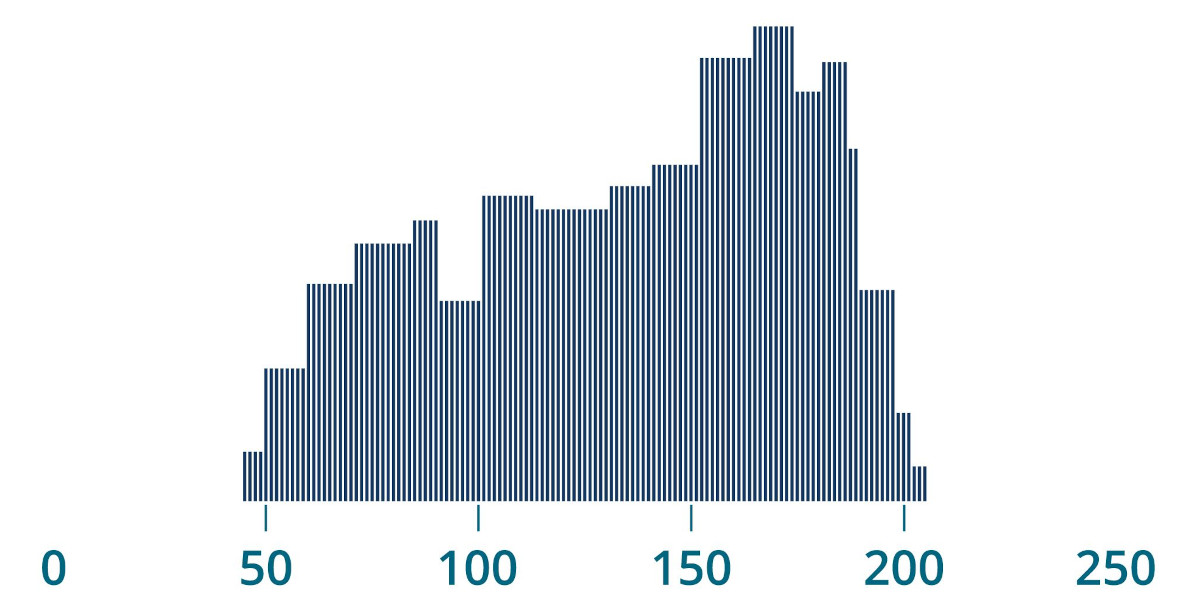
ヒストグラムはデータを等分して、区分ごとの数値を棒グラフで表したものです。「度数分布図」とも呼ばれ、データの分布状況やバラつき、ピーク値などを把握できます。一般的に離れ小島のように外れた位置にグラフの山ができている場合には、異常が発生した製品のデータの可能性が高いとされています。
たとえば、製品の重量をヒストグラムで表すと、想定していた誤差に対して、実際はどの程度のバラつきがあるのか、視覚的に把握できます。
散布図
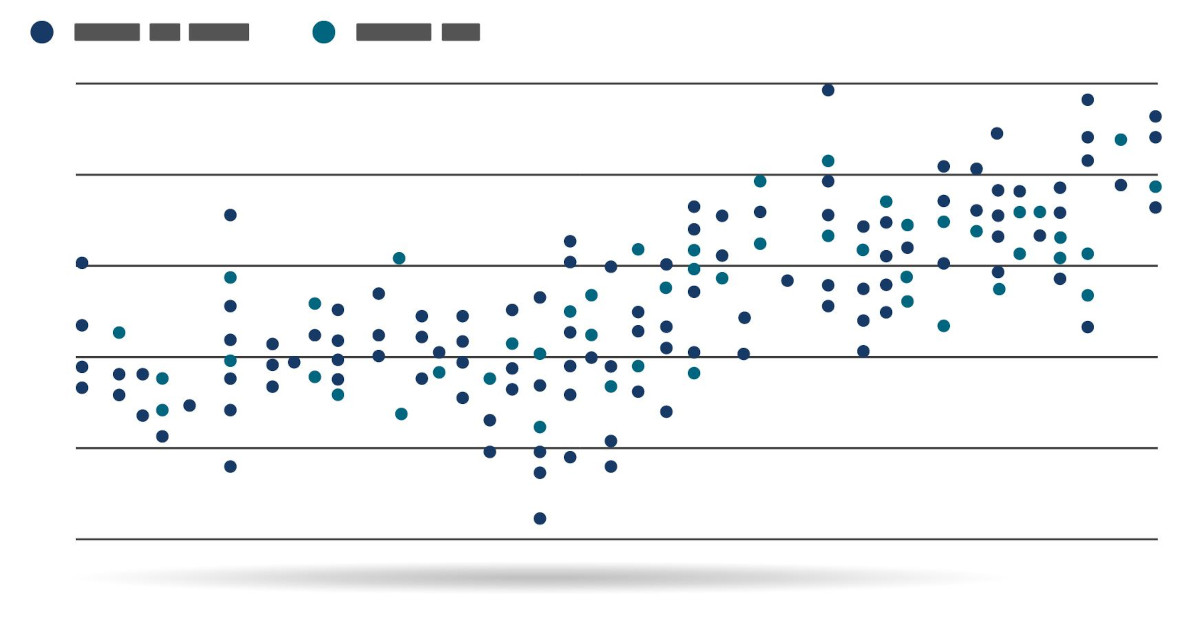
散布図は、横軸と縦軸で2つの項目の数値をとり、交点を点で表したものの集合です。散布図は2つの項目に相関関係があるか分析するときなどに使われており、散布図の点の相関関係は主に3パターンがあります。
- 右上がりの相関:正の相関。横軸の数値が増加していくにつれて、縦軸も増加していく
- 右下がりの相関:負の相関。横軸の数値が増加していくと、縦軸は減少していく
- 無相関:縦軸と横軸の数値の増減に法則性がなく、2つの項目の相関関係が見い出せない
たとえば、横軸に材料の厚み、縦軸に強度の数値をとって散布図をつくり、右上上りになっていると、材料が厚いほど強度が強いという相関関係があることがわかります。
管理図
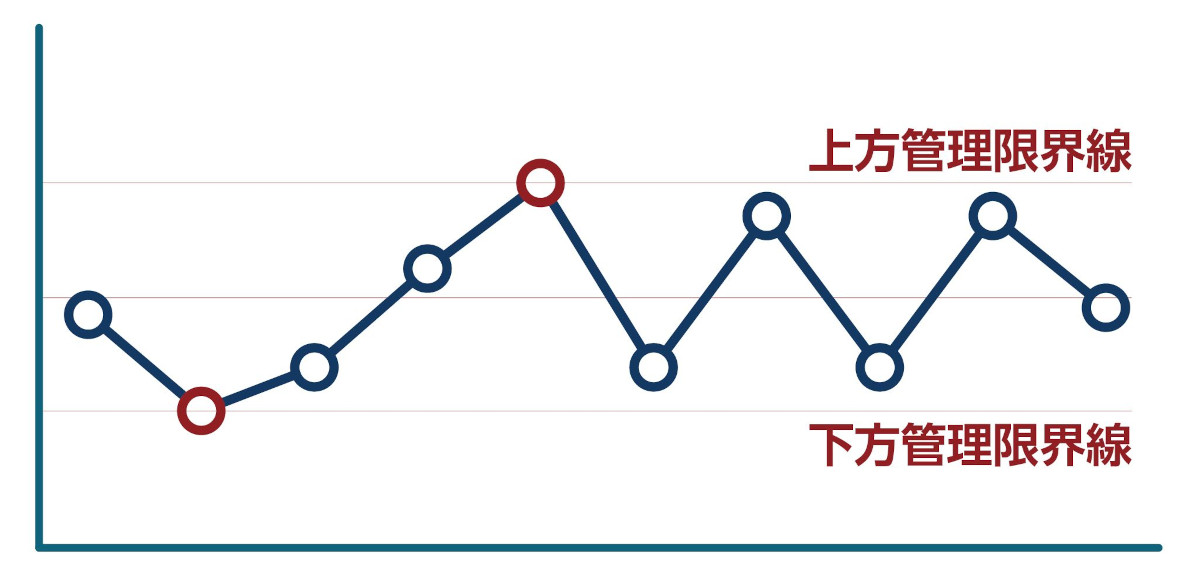
管理図は品質のバラつきの変化を時系列で表し、工程の安定性を確認するための図です。
まず、品質の特性に関する時系列のデータを折れ線グラフで作成します。次に品質の特性の平均値を中心線として引き、上下に基準内の限界を示す上方管理限界線と下方管理限界線を引きます。そして、上方管理限界線と下方管理限界線を超えた値を異常値として、原因の究明を図る対象とします。
たとえば、製品不良の発生個数が管理限界線を超えている地点が把握できれば、その時点でどういったことが起きたのか調査して原因を究明し、対策を講じます。
チェックシート
チェックシートは設定した項目ごとに、点検や記録を行っていくための表です。決まった形式はありませんが、製造業では「点検用チェックシート」や「記録用チェックシート」などがよく用いられています。
- 点検用チェックシート:作業項目の漏れをなくすためのシート
- 記録用チェックシート:パレート図を作成するケースなど、データ収集を目的としたシート
たとえば、製品不良の主な原因を把握したい場合には、原因の種類を項目として立てた「記録用チェックシート」を作成します。
新QC7つ道具(N7)とは
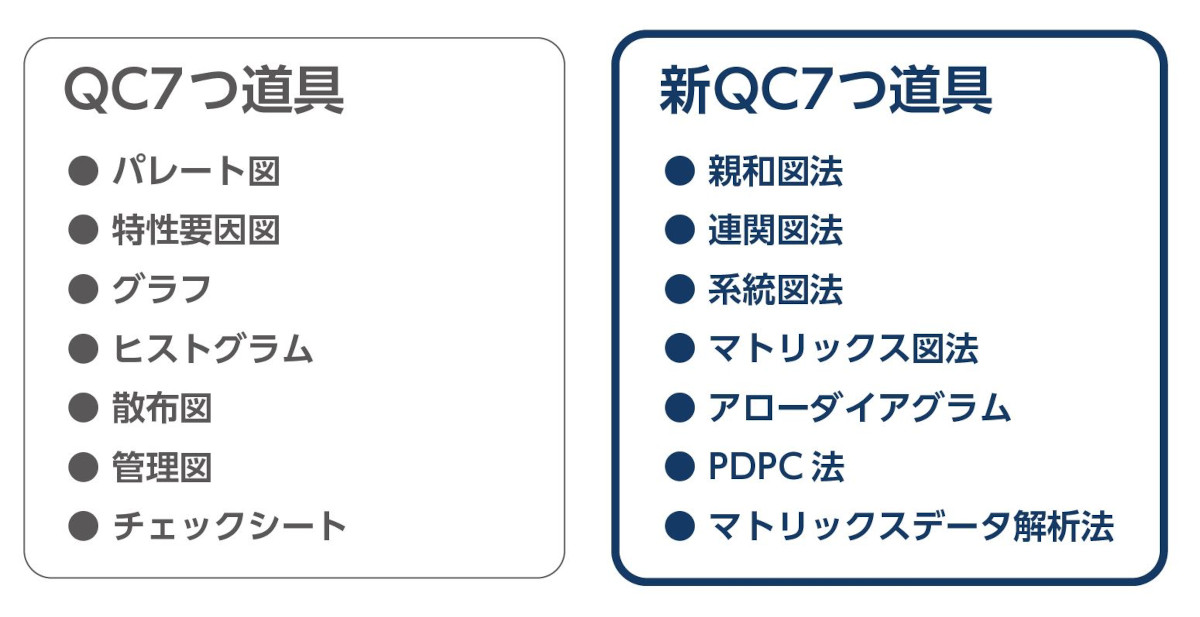
QC7つ道具とは別に、新QC7つ道具と呼ばれる手法も浸透しています。QC7つ道具は数値データ、すなわち定量データを用いるのに対して、新QC7つ道具は主に言語データという定性データを活用することが大きく異なる点です。
新QC7つ道具は数値化が難しい問題を解決するために生まれた手法で、言語データを図や表にわかりやすくまとめていきます。また、QC7つ道具は主に製造現場で活用されていますが、新QC7つ道具は企画や設計、営業といったより広い部門で活用されています。
なお、新QC7つ道具は英語で「New seven tools for QC」あるいは「New 7 QC Tools」と名付けられていることから、「N7」と略されて呼ばれることもあります。
次に挙げる新QC7つ道具の手法について、個別に解説していきます。
- 親和図法
- 連関図法
- 系統図法
- マトリックス図法
- アローダイアグラム
- PDPC法
- マトリックスデータ解析法
親和図法
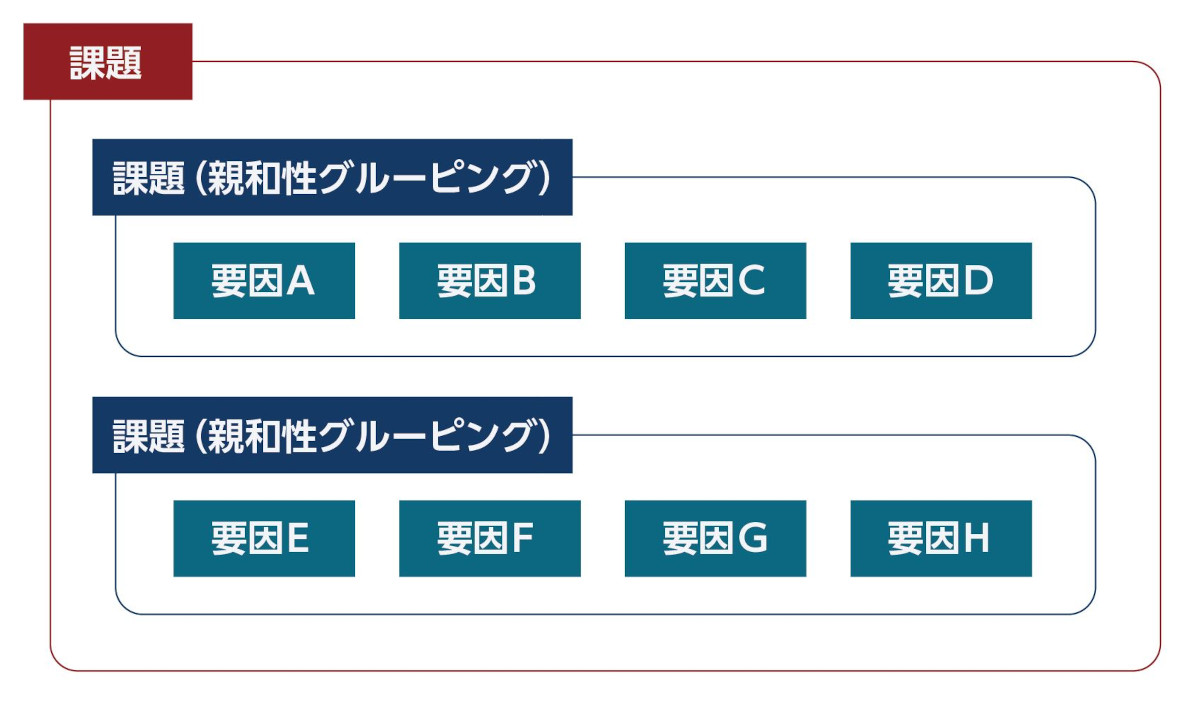
親和図法は、将来起こりえる問題やはっきりと全貌がわからない課題などの構造を明らかにするための手法です。課題の要因を親和性にもとづいてグループ分けをして、体系化します。これにより、課題の全体構造や特徴、取り組むべき課題を明確にしていくものです。
連関図法
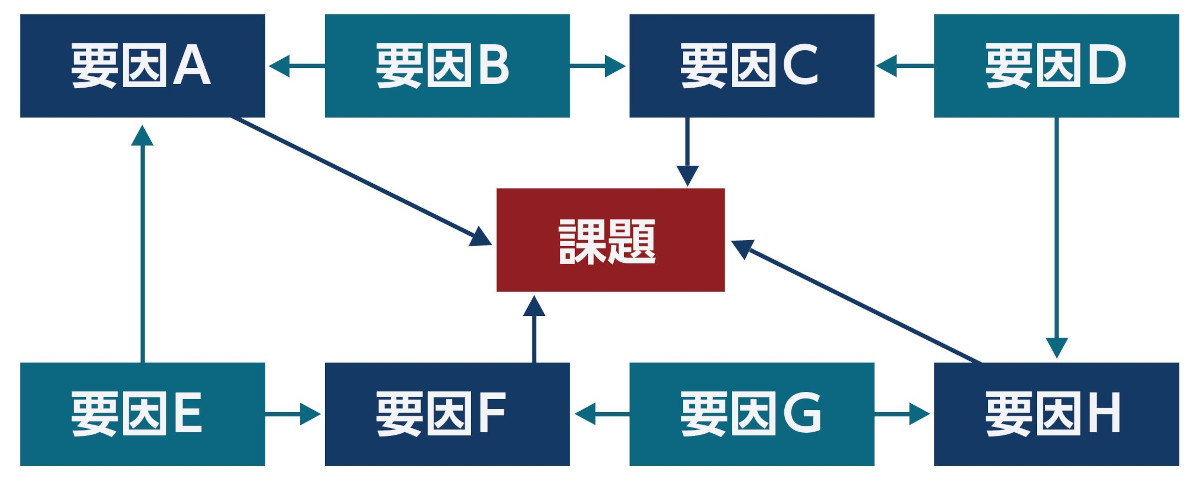
連関図法は複雑に問題が絡みあっているケースなど解決方法が見い出せないときに、因果関係をもとに問題を明らかにする手法です。要因を書き出し、たとえば、要因と手段、要因と結果など、因果関係がある要因と要因を矢印でつなぐことで、主要因を導いていきます。
連関図法はQC7つ道具の特性要因図と似ているところもありますが、要因同士のつながりも探っていくという点で異なります。
系統図法
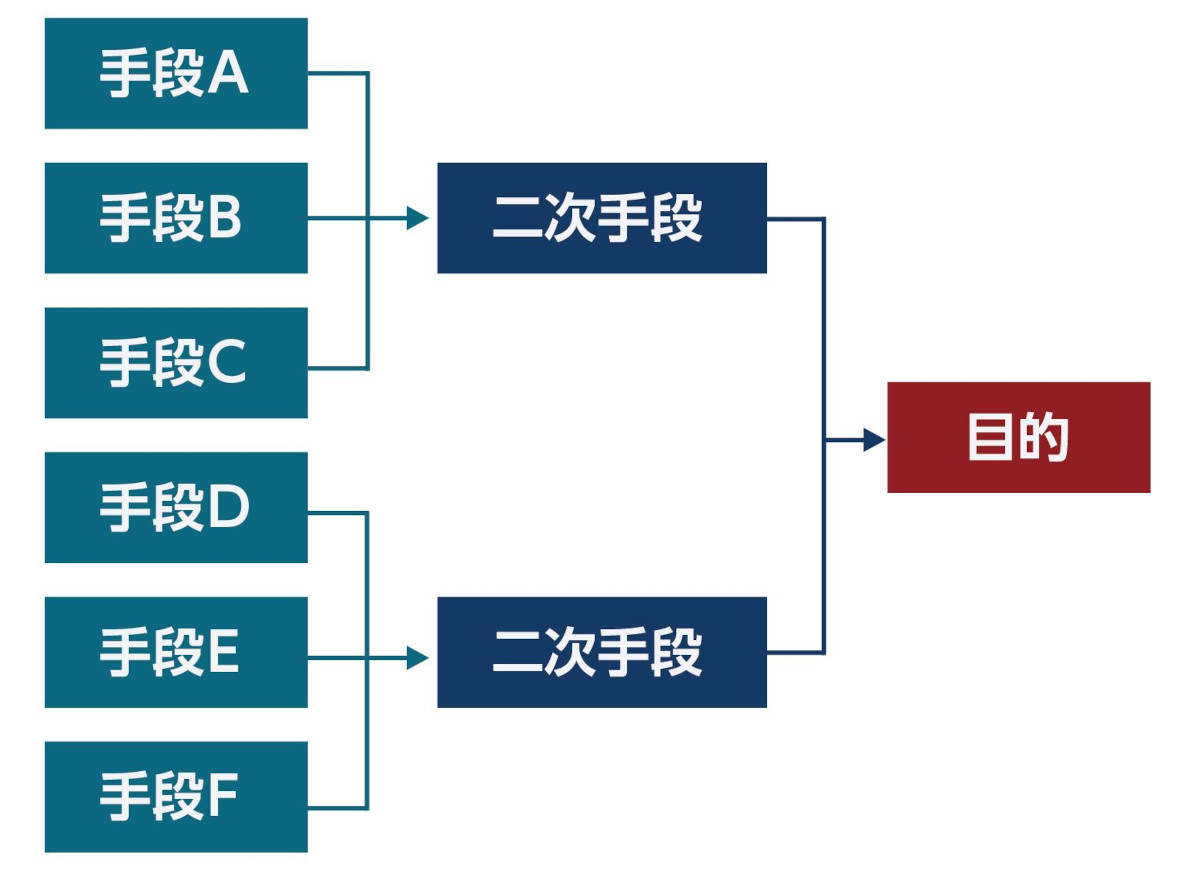
系統図法は目的を達成するための手段をツリー状に配置する手法です。まず、目的を設定し、次に目的を達成するための一次手段を設けます。そして、次に一次手段の達成を目的として、二次手段を検討します。
さらに二次手段の達成を目的として、三次手段、四次手段といった形で繰り返し、作成したツリー状の図をもとに、最適な手段を導き出すというプロセスです。
マトリックス図法
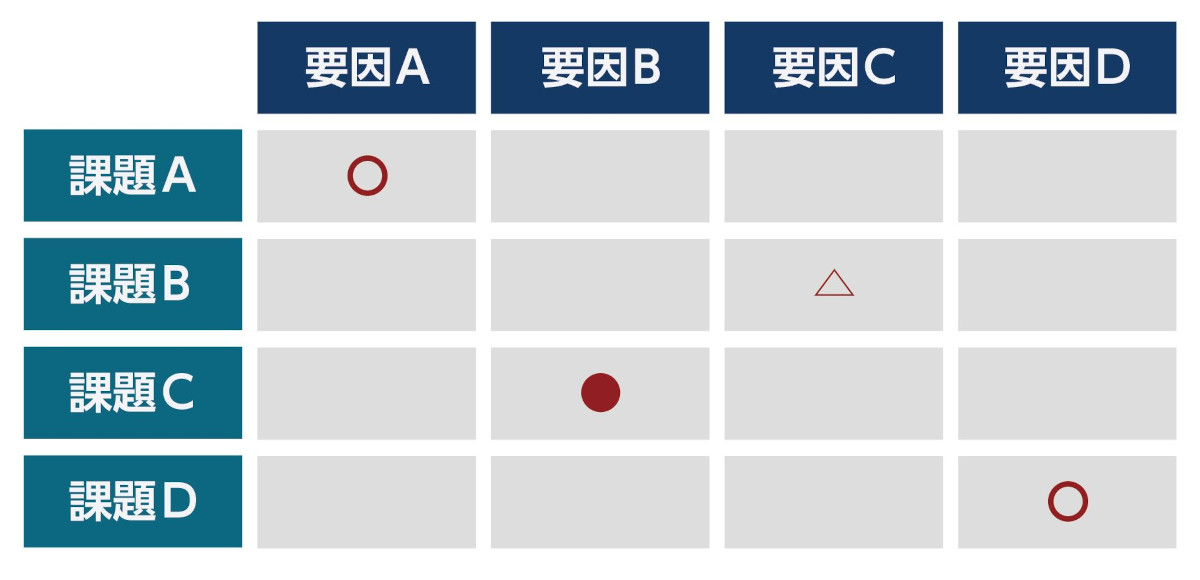
マトリックス図法は2つの要素を縦軸と横軸に配置し、交点に関連度合いを評価して記入していく方法です。要素同士の関係性を整理したいときや全体を俯瞰して検討したいときなどに用いられています。
また、QCにおいては系統図法で検討した手段の優先順位や役割分担の決定にも使われている手法です。
アローダイアグラム
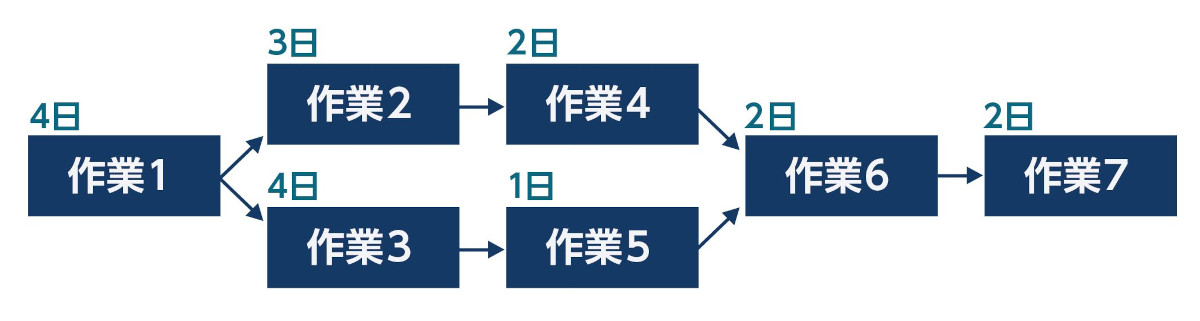
系統図法やマトリックス図法で、実施する手段や優先順位を決めた後、実際に実施する順番や日程を決めるのに用いられるのがアローダイアグラムです。
アローダイアグラムは各作業を矢印で結び、作業日数も記載することで、作業の順序関係やつながり、全体のスケジュールを明確にして管理を行っていく手法です。作業に着手する前に、作業日程に関する問題も把握できます。
PDPC法
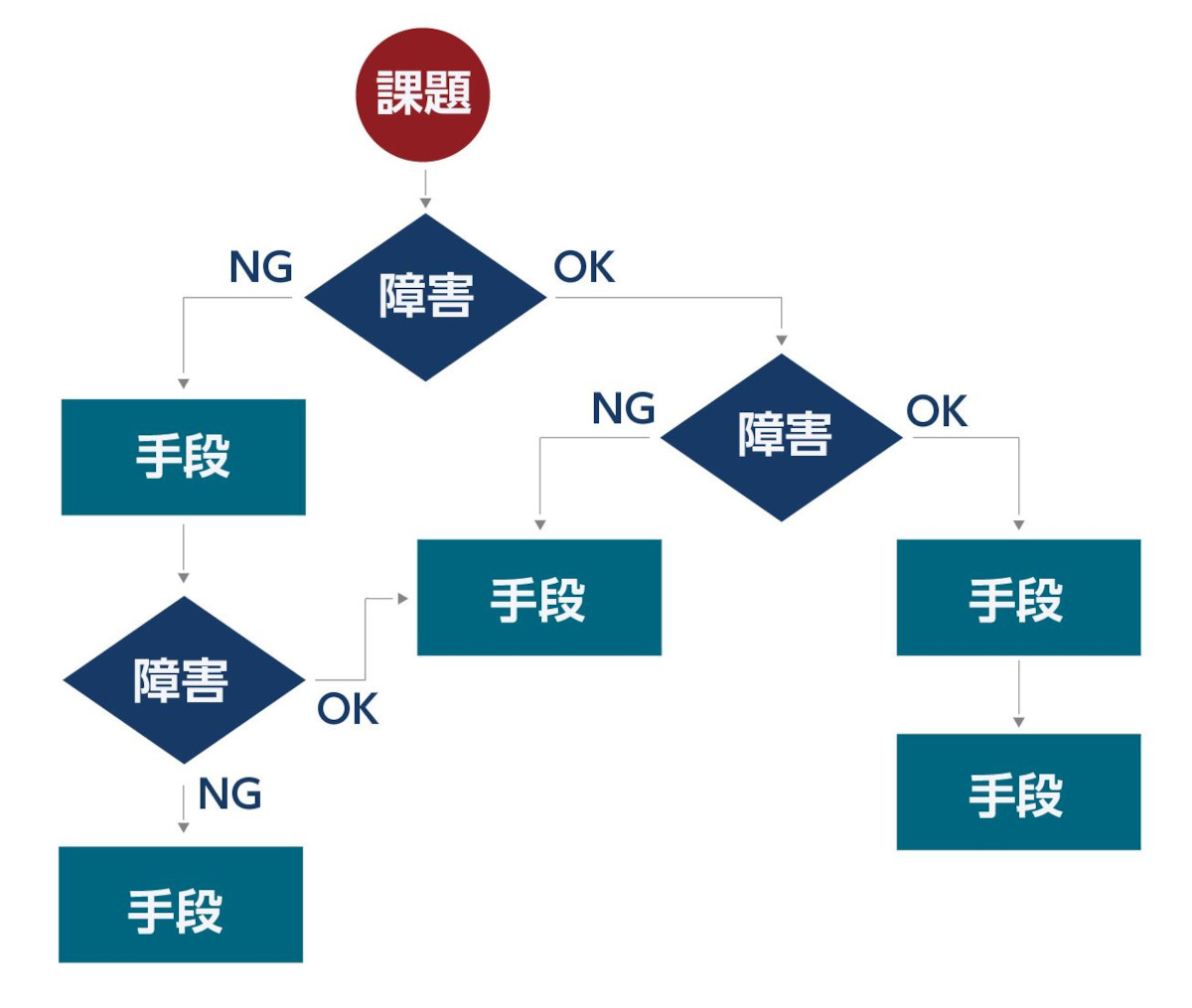
PDCP法は「Process Decision Program Chart」の略称で、日本語では「過程決定計画図」と呼ばれています。目標達成までに障害となる可能性があることを予測し、代替案を明確にしておく手法です。
PDCP法ではゴールまでのプロセスのルートをチャートで示していきますが、2つの手法に分けられます。
- 強制連結型PDPC:ルートとゴールを必ず結びつける手法。手順が大枠で決まっている場合に用いる
- 逐次展開型PDPC:不測の事態が起きたときに都度、打開策を考えていきながら、ゴールに辿りつくルートを探っていく手法
マトリックスデータ解析法
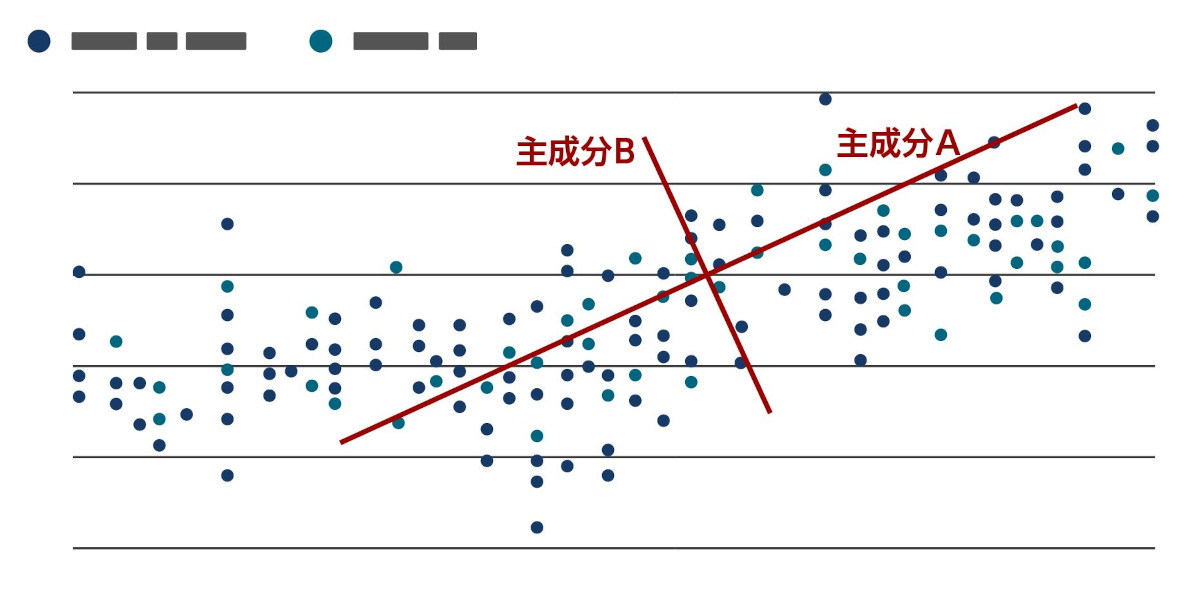
マトリックスデータ解析法は、新QC7つ道具の中で、唯一数値データを使う手法です。数値データを縦軸と横軸の2つの評価項目から散布図で表し、主成分分析という統計学の手法で分析します。
マトリックスデータ解析法は数値データの特徴を把握するために用いられています。
まとめ
定量的なデータ分析を用いるQC7つ道具の活用で、定量的な観点からの品質担保が可能になります。仮説を立案し現状を把握し、課題の要因を特定。さらに改善策を実施した後は効果検証を経てPDCAサイクルをまわすプロセスは、定着化およびブラッシュアップにも有効です。
QC7つ道具や新QC7つ道具はQCサークルの資料作成にも活かせる手法です。品質管理における課題解決に向けて、QC7つ道具を取り入れることを検討してみましょう。
また、日研トータルソーシングでは、派遣スタッフに向けて品質管理に関する資格取得の全社サポートを展開しています。
【主な資格取得実績】
- 品質管理検定(QC検定)
- 自主保全士
- 機械保全技能士
- 衛生管理者
さらに、コスト削減や作業時間短縮、不良率の低下など、QC活動を通じた改善事例をナレッジとして蓄積。お客様へご提案させていただくとともに、品質・生産性向上を支援しています。
QC活動および品質管理オペレーションのポイントとなる設備保全業務をはじめ、製造現場の人材不足解消に向けた、弊社独自の取り組みをまとめた資料もご用意しています。アウトソーシングをご検討されている企業の皆様は、ぜひ御覧ください。